TRIBOLUBE 16 8oz Tube
Product details
TRIBOLUBE 16
Tribolube 16, 8-Oz. Tube
Tribolube-16 is a wide temperature range grease especially useful in vacuum and other systems where nonreactivity with chemicals, strong acids and oxidizers, fuels, and solvents is required. Although this lubricant is very inert, newly exposed rubbing surfaces of aluminum and magnesium may react with the greases under certain conditions.
Care and Storage Instructions
- After use, wash in fresh water and allow to dry in a well ventilated area out of direct sunlight
- Store in a well ventilated dry area away from direct sunlight
Specifications
TRIBOLUBE 16 8oz Tube
Specifications
Packaging | 8-Oz. Tube |
Tribolube Series | Tribolube 16 |
Market | Aerospace / Automotive OEM |
Type of Lubricant | Fluorinated Polyether Grease |
NLGI No. | 2 |
Temperature Range | -45 to 400 °F |
Unworked Penetration @ 77°F | 299 |
Worked Penetration @ 60 Strokes | 300 |
Evaporation 22 hrs @ 350°F | 1.00 % |
Evaporation 22 hrs @ 400°F | 5.30 % |
Copper Corrosion 24 hrs @ 212°F | 1a |
Mil Specs | MIL-G-27617 MIL-G-27617D MIL-G-27617D (Types 2 and 3) MIL-PRF-27617 MIL-PRF-27617 (Types 2 and 3) |
Oil Separation 30 hrs @ 400°F | 10.45 % |
LOX Impact Sensitivity 20 impacts from 43.3 in | No Reaction |
Water Washout- 1 hr @ 105°F | 0.8 % |
Steel-on-Steel Wear @ 1200 rpm. 40 kg. 400°F. 1 hrs. 52100 steel | 1.07 mm |
High Temperature Performance @ 400°F. 20000 rpm. 5 lbs | >600 hrs |
High Temperature Performance @ 400°F. 10000 rpm. 5 lbs | >2000 hrs |
High Temperature Performance @ 425°F. 10000 rpm. 5 lbs | >2000 hrs |
Low Temperature Torque @-30°F. Starting | 1885 gm-cm |
Low Temperature Torque @-30°F. 60 min. Running | 1235 gm-cm |
Low Temperature Torque @-40°F. Starting | 6500 gm-cm |
Low Temperature Torque @-40°F. 60 min. Running. | 2925 gm-cm |
Low Temperature Torque @-45°F. Starting | 16575 gm-cm |
Low Temperature Torque @-45°F. 60 min. Running | 14300 gm-cm |
Film Stability and Steel Corrosion 168 hrs @ 212°F | Pass |
Resistance to Aqueous Solution 168 @ 77°F | Pass |
Fuel Stability @ 77°F | 0.20 % |
Fuel Resistance 8 hrs @ 77°F | Pass |
Type | 16 |
Applications
This grease is suitable in applications including small and large diameter ball, roller, needle, and plain bearings, electrical contacts, threads, valves, gears, contacts, splines, ball screws, and screw actuators. It is compatible with most elastomers and plastic seals, gaskets and O-rings.
Fundamentals
Function of Lubricating Greases
A good quality lubricant reduces friction and wear, dissipates heat, keeps out dirt, and prevents rust formation. It must provide good "boundary layer" lubrication, and be thin enough to get between moving parts, and once there, it must be thick enough to separate them with a slippery oil film. This oil film must be strong enough to provide full-film "hydrodynamic" lubrication between moving parts such as bearings, screw actuators, etc. It must also act as a kind of floating seal, filling in the microscopic imperfections in moving surfaces with a thin film of lubricant.
If it is too thin, under shock or extreme loads it will not separate moving surfaces. If it is too thick, it cannot squeeze between the moving parts to provide proper lubrication. If either extreme exists, friction and wear occurs; accumulating wear debris escalates wear until failure occurs.
Heat is generated between moving parts in machines, even though they are lubricated. Some greases can reduce the operating temperatures of bearings , gears, or other moving parts by having better EP and anti-wear properties thereby reducing the metal to metal contact and the associated heat. Grease lubricants also work as a seal, keeping out dirt and other foreign matter, thus preventing damage to the bearing and contact surfaces. The effect of rust or corrosion on unprotected metal can readily be understood. A lubricating film on moving parts protects them from this damage by preventing contact with air, moisture or other corrosive agents thereby increasing useful life.
Properties of Synthetic Lubricating Greases
In general, a grease is an oil that has been thickened by a solid or semisolid dispersion, commonly a clay or a soap, in a petroleum or synthetic lubricating fluid, plus the desired additives used to enhance grease performance properties.
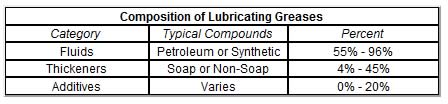
All of the grease components affect the physical and chemical properties. Standardized testing must be used to provide useful information about the properties of grease lubricants. Such information can then be used to compare and select a grease for a specific application. Some of these tests are described in following sections.
Purpose of Synthetic Lubricants
Demands placed upon lubricants have become increasing severe with advances in industrial machinery and equipment design. Higher operating temperatures, speeds and gear and bearing loads are stressing the capabilities of conventional petroleum-based lubricants. The OEM's have increased demands for "sealed for life" applications. Such applications require synthetic lubricants.
Synthetic lubricants were developed to meet demanding requirements which exceed the operational limits of conventional petroleum based lubricants. Because they are man made, synthetics can be better tailored to their role as a lubricant by meeting predetermined physical and chemical properties. Formulated from pure hydrocarbons, synthetics do not contain the impure components that adversely affect the physical and chemical stability of petroleum based lubricants.
Synthetic oil and grease lubricants have been solving demanding lubrication problems by replacing petroleum lubricants in applications that exceed their environmental, operational, or service life limitations. In such applications, synthetics pay for themselves many times over in reduced component failure, repair costs, warranty costs, down time, and increased service life.
Synthetic vs Petroleum Lubricants Performance Both oil and grease lubricants made from syntheticbased fluids have a much wider operating temperature range and are more thermally and oxidatively stable than lubricants made from petroleum-based fluids. Low Temperature Performance
At very low temperatures, most petroleum-based oil and grease lubricants thicken and are usually limited to temperatures no lower than -20ºF unless high temperature performance is sacrificed. In contrast, synthetic oil and grease lubricants have good low temperature viscosity and fluidity characteristics down to as low as - 140ºF, and are still capable of operating at temperatures as high as 600ºF.
High Temperature Performance
Lubricants are susceptible to failure at high temperature, especially in thin films after long term exposure. Recent research in boundary lubrication confirms the primary role of high temperature in lubricant degradation. Increasing temperature rather than increasing shear load has been found to induce most lubricant failures. Petroleum-based oil and grease lubricants have an upper temperature limit of about 250ºF to 300ºF. Above these temperatures they become fluid and volatile. If grease lubricated machinery is operated above that temperature limit, the lubricant breaks down and may melt or form hard carbon deposits. Some synthetic grease lubricants can operate up to about 600ºF without melting.
Oxidation Stability
Oxidation is the primary breakdown mode of most lubricants, leading to the formation of sludge and other corrosive compounds. When lubricants are exposed to air, oxygen, or other strong oxidizing chemicals, petroleum- based lubricants deteriorate and break down easily, especially at high temperatures. Many chemicals can attack petroleum-based lubricants resulting in gummy deposits. Lubricant failure may result in corrosion of parts, deterioration of seals, stuck or worn bearings, and product contamination. This results in frequent equipment down time for relubrication, replacement of parts, cleaning, and maintenance. The thermal and oxidative stability of synthetics often makes them the only alternative for very cold, extremely hot, sealed for life applications, or harsh operating environments.
Dust, dirt, and other debris can create additional problems for petroleum-based lubricants. These lubricants tend to attract contaminates because they are naturally occurring compounds which have unreacted molecular end groups. These end groups produce electrical charges at the surface, so when a charged dust or dirt particle comes near, they are attracted to the surface of the lubricant. The dust particles can be abrasive and damage parts and machinery. It is this characteristic of petroleum-based lubricants that create problems in dusty and dirty applications such as paper and textile mills, printing plants, and metal-forming operations. This situation leads to frequent machine down time for cleaning and relubrication. Because synthetics are man made, they are fully reacted chemicals and do not have the unreacted end groups which attract dust and dirt. Wear of moving parts can thus be reduced in dusty environments.
Load and Wear Performance
Synthetics lubricants can provide increased wear protection over petroleum-based lubricants due to better viscosity-temperature properties. Tribolube Synthetic Lubricating Oils and Greases are specially formulated to function in applications or environmental conditions where standard "general purpose" lubricants will not perform or will perform only marginally. Tribolube lubricants outperform conventional lubricants under conditions such as hard vacuums, low and high operating temperatures, oxidizing environments, high rotating speeds, extremely high load conditions, applications where little wear can be tolerated, high radiation levels, extremely corrosive environments, and where long life is mandated.
What are the Pay Offs?
The failure of petroleum lubricants to give adequate performance is making greases and oils formulated from synthetic hydrocarbon fluids increasingly attractive. Reduced maintenance costs for manpower and replacement parts, and reduced downtime with associated production loss, make synthetic lubricants cost effective in most applications. The demand for lubricant stability over increasingly wider ranges of operating conditions exceeding the capability of petroleum lubricants is making synthetics mandatory in many OEM applications. The failure of petroleum lubricants to give adequate performance is making greases and oils formulated from synthetic hydrocarbon fluids increasingly attractive. Reduced maintenance costs for manpower and replacement parts, and reduced downtime with associated production loss, make synthetic lubricants cost effective in most applications. The demand for lubricant stability over increasingly wider ranges of operating conditions exceeding the capability of petroleum lubricants is making synthetics mandatory in many OEM applications.